What is polyketone?
Aliphatic polyketone, often referred to as just polyketone or PK, is a semi-crystalline engineering resin that is an alternating copolymer of carbon monoxide and ethylene with some propylene (1–10%). It has good tensile, thermal, flex, and impact properties like nylon (PA), while maintaining the excellent wear, chemical resistance, and dimensional stability of acetal (POM).
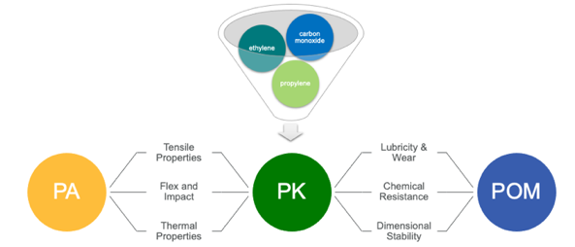
Although polyketone is a relatively new class of polymer, it is growing in popularity as application engineers seek high-performing alternatives to nylons and POM amid supply constraints and sustainability goals.
How is polyketone different?
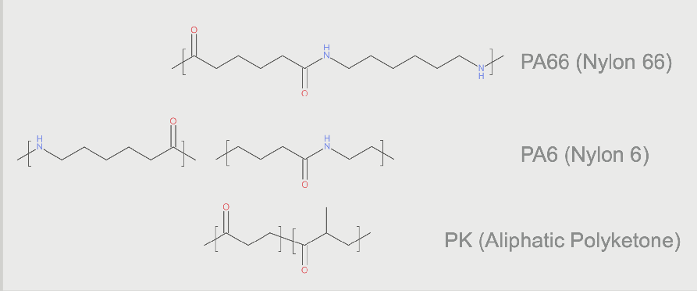
In the chart above, you can see the polymer structure of polyketone is very similar to PA6, PA66, and POM, which explains the similarity in properties. All are semi-crystalline materials that contain an abundance of carbon and oxygen. Polyketone has a carbon backbone consisting of polar ketone groups, however, polyketone lacks the nitrogen present in the amide bond of the nylon backbone. This makes PK much less hygroscopic than PA6 and PA66, and the resulting properties are much less sensitive to moisture conditioning. POM is based on polymerized formaldehyde, which makes the polymer sensitive to thermal degradation, releasing formaldehyde gas. On the other hand, the PK structure is based on copolymerized carbon monoxide and ethylene, which is more thermally stable than POM and does not release formaldehyde as it thermally degrades. Interestingly, perfectly alternating polyketone copolymer results in a highly crystalline material that is very difficult to process. A small amount of propylene is added during the polymerization as an engineered defect to improve the processability.
Offering a Sustainable Nylon Alternative
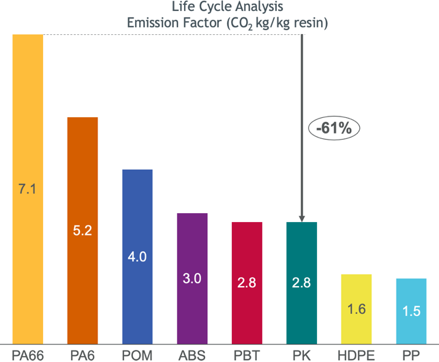
Polyketone is considered “eco-conscious” due to the reduced environmental impact of this base resin during the production process compared to PA6, PA66, and POM. According to third-party life cycle analysis (LCA), there is a 61% reduction in CO₂ compared to PA66. This is due to the low carbon footprint of the monomers, which is similar to that of traditional polyolefins. With PK, you can get engineered thermoplastic performance with an added benefit of a polyolefin carbon footprint.
Why Chose Polyketone Over Nylon?
Comparing Material Properties of Polyketone vs Nylon
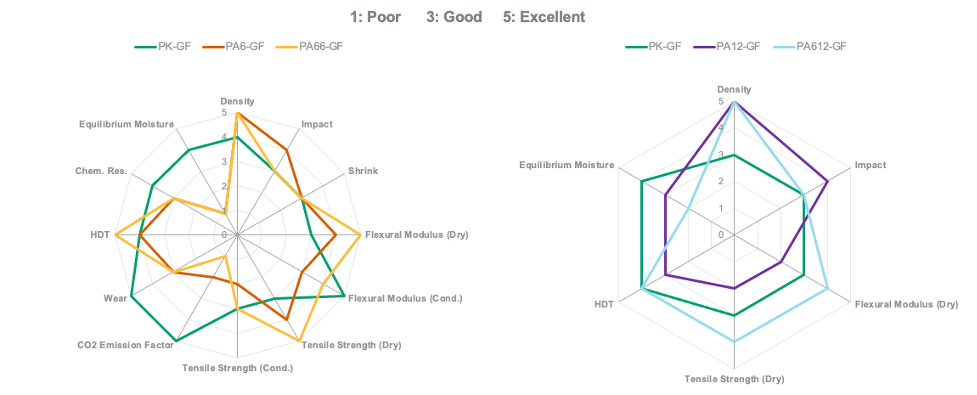
Polyketone, either as a filled or unfilled formulation, is often compared to PA6 & PA66, but it’s also an attractive replacement for more specialty long-chain, low moisture nylons like PA12 and PA612. The chart above demonstrates the performance characteristics of these materials. In each comparison, polyketone thermoplastics offer product engineers and designers a new tool in the product development toolbox for engineering plastics. The material selection decision, however, will be dependent on which properties are most important for the specific application.
Moisture Resistance Testing of Polyketone
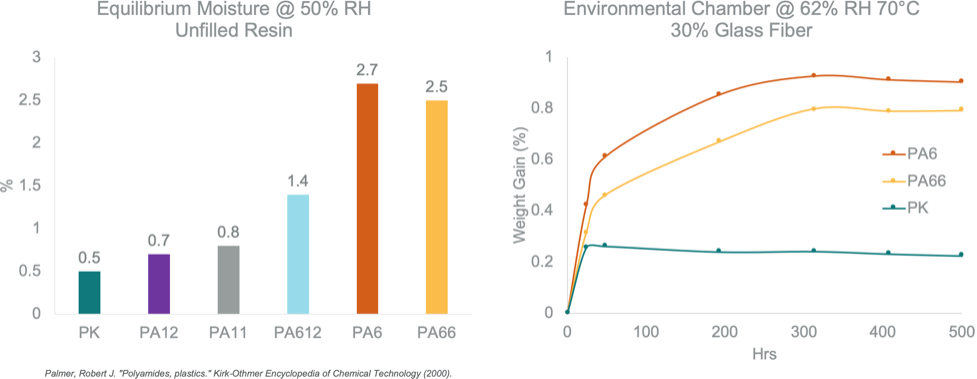
Humidity and moisture can have an effect on material performance in both the short- and long-term scenarios. Therefore, specialty nylons like PA12 & PA612—with longer, more hygroscopic carbon chains present in their backbone—are often used in applications that cannot tolerate property change with ambient moisture conditioning.
However, as previously mentioned, polyketone is much less hygroscopic than PA6 & PA66 due to the lack of nitrogen in its polymer structure. In fact, the equilibrium moisture of PK is even lower than the long-chain nylons, making it a good alternative for moisture-rich environments.
The charts above compare 30% short glass-fiber filled samples and show a noticeable difference in the moisture uptake behavior of PK versus to PA6 & PA66. Whereas PA6 & PA66 show an initial jump in moisture uptake followed by a gradual increase, PK shows a rapid but lesser increase that quickly plateaus.
Moisture Conditioning Comparison
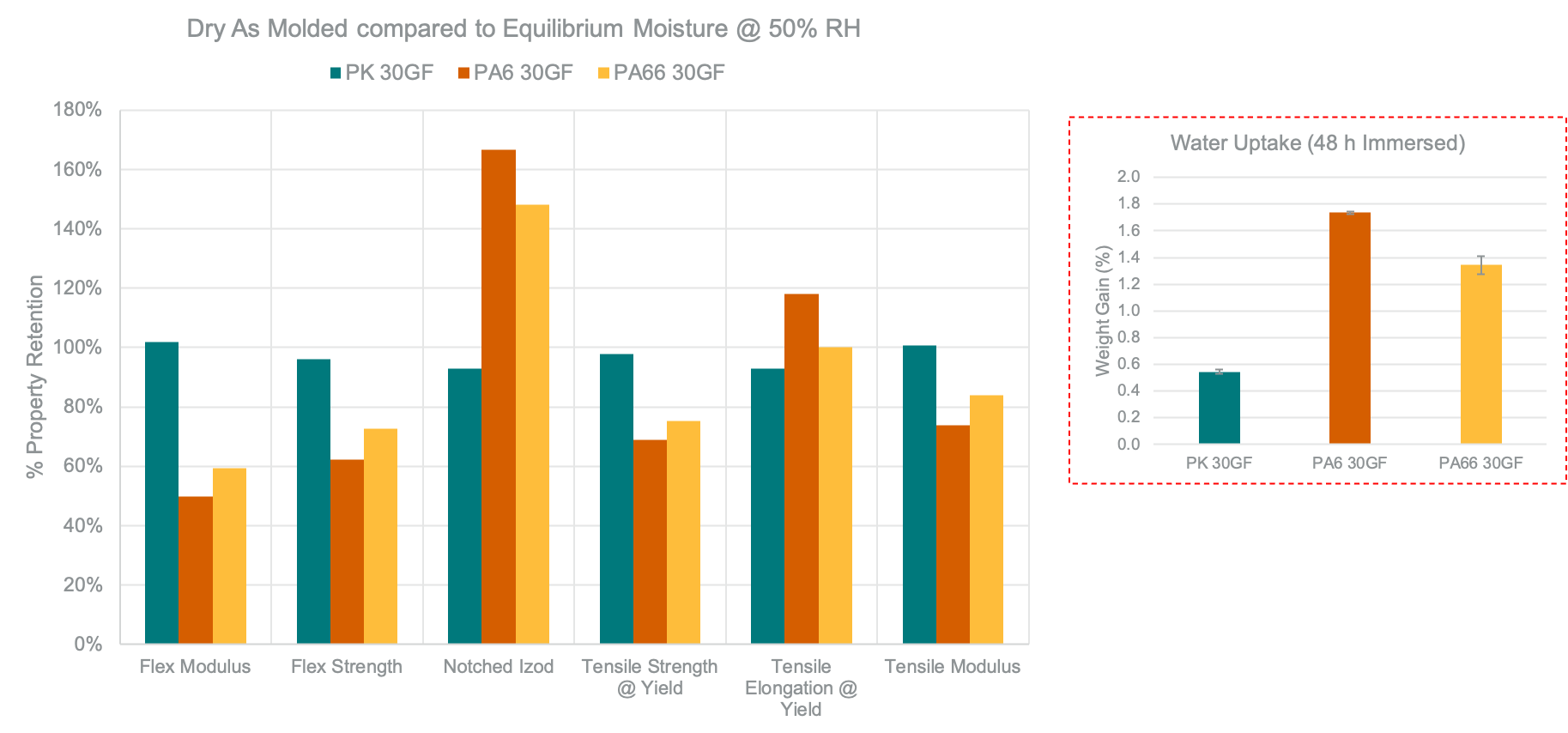
The difference in moisture uptake is also evident in property change between samples tested dry as molded compared to equilibrium conditioned, as shown in the chart above. Compared to glass-filled PA6 & PA66, moisture does very little to affect the physical property change of glass-filled PK. A noticeable difference here is impact properties, which are improved for nylons since water plasticizes nylon and makes them more impact resistant.
Understanding Chemical Resistance
One of the other key values of polyketone thermoplastics is their incredible chemical resistance, especially in contrast to aliphatic and aromatic hydrocarbons. The image below demonstrates the outcome against 30% sulfuric acid.
30% H₂SO₄, 24 HRs, 23°C
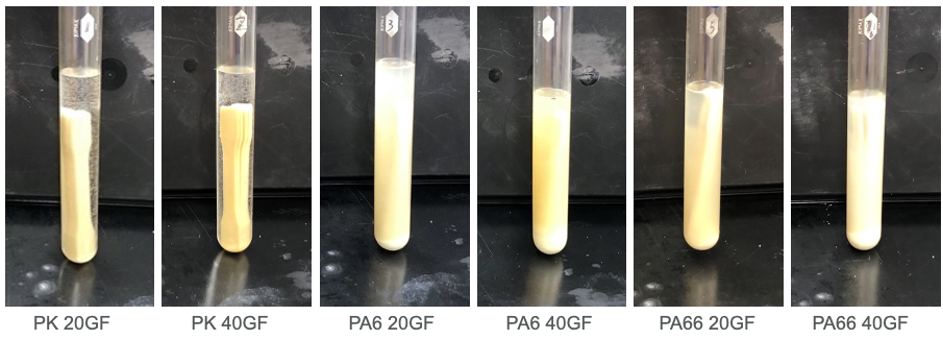
Glass-filled PA6 & PA66 test bars dissolved within one day, while the glass-filled PK samples remained stable after 20 days. Avient also soak-tested its performance against other chemicals including 10% hydrochloric acid, 10% calcium chloride, antifreeze, 10% ammonium hydroxide, 12% sodium hypochlorite (bleach), and ethanol. In each case, the physical property retention of Avient’s PK-based formulations was superior to that of PA6 or PA66.
Long-Term Chemical Resistance Testing
40% Glass-Filled Resin
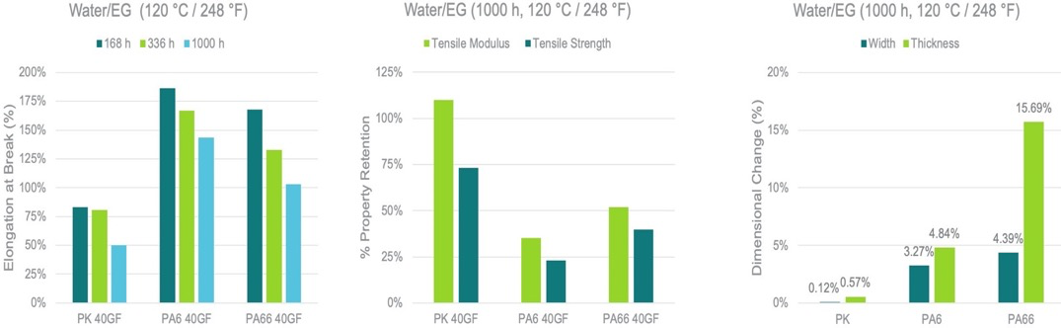
Polyketone’s chemical resistance is excellent even at elevated temperatures and long durations. In the chart above, samples were tested for 1,000 hours at 120°C against water/ethylene glycol mixtures, more commonly known as antifreeze. The glass-filled polyketone samples showed better property retention and lower dimensional change than PA6 and PA66.
Can PK be colored and what are the limitations?
Although polyketone thermoplastics have an abundance of performance benefits and advantages, a common limitation of this base resin can be aesthetics and colorability. Polyketone is naturally a burnt orange color and is known to be more challenging to color. However, Avient has overcome this challenge and achieved vibrant colors like any other resin. Here are a few things we learned when coloring PK.
- Good surface aesthetics and color retention are maintained after sterilization processes.
- Scratch and mar performance is average but not as good as some engineered nylon 6 or 66 resins. However, it surpasses ABS, COPET and PC alloys.
- If the material is allowed to stay in an injection molding machine or extruder (profile, sheet, etc.) too long, the material will start to discolor and brown ‘freckles’ may appear.
- Standard PK materials have a lower gloss level than nylons or other standard engineered resins. The gloss level cannot be improved through process modification and only small improvements can be made with a change in the tooling surface.
- Similar to other resin systems, the addition of a color pigment may lower mechanical properties.
- These can be colored at the press or with pre-color. When coloring at the press, the carrier is critical for compatibility to mitigate issues with property retention, gloss, and surface issues like streaking.
Common Questions
As mentioned earlier, polyketone is relatively new and not yet as common as traditional engineered resins like nylons or acetal. Here are some questions you may be asking as you consider the performance needs and application challenges you face.
What is the heat aging performance of PK?
What is the creep rupture resistance versus the nylon-based offerings?
How well does this material work with adhesives for bonding?
Are UV protection and/or flame retardant packages available?
What is the lead time for these materials?
Get the answers to these questions by downloading our PDF Guide to Polyketone overview brochure. For more insight into processing polyketone, such as shrink rate, run temperature, and drying conditions, check out our processing guide PDF.